Nine brickmaking sites in Cuckfield
- gmdavison
- May 27, 2022
- 6 min read

If you asked a local resident 'what industrial production would you associate with Cuckfield' the most likely products that would be suggested might be leather tanning, possibly timber, but more likely iron - but few would mention brick manufacture. But the expansion of housing and building in general led to a widespread use of onsite brick production.
Cuckfield like most towns in the area - especially in the growth period of the nineteenth century - if viewed from above would be seen with smoke billowing from brick kilns and clamps. For weeks on end at construction sites, close to the centres of habitation, smoke must have been getting into the eyes and onto the clothes of local residents. This production not only polluted the atmosphere but also presented health risks for the brickmaking workforce.
Nine brickfields have been identified in the Cuckfield area, but probably there are more that have gone unrecorded. They were opened up to meet a specific need then, when they ran out of clay or sufficient bricks had been produced, they would have been returned the production site to fields or been built on.

When the brickfields proved inadequate to meet the needs of a larger project, materials could be transported by road from further away, even imported from abroad through local ports. But this would be limited by the delivery capacity of horse and carts (500 bricks at a time) and the extra cost of the haulage.
Bricks from The Netherlands
Large loads of high quality bricks were needed for the Ouse Railway (Balcombe) Viaduct and were imported from The Netherlands. They made their way by barge to beneath the viaduct itself along the Ouse canal.
The term 'brickyard' implied the presence of a kiln, whereas a site where a 'brick clamp' was used, was usually referred to as a 'brickfield'. The latter were often short lived. A property developer would buy land, create a brickfield close to or on the site. Sometimes the first houses built and brick production would be moved to another part of the site.

Railway construction and local brickyards
Railway contractors preferred to source their own supply of bricks - and sometimes using the new railway line as a means of bringing in material to the site.
Henry Michell, a Horsham brewer bought land in Three Bridges in 1838 and opened a brickfield when work on the London to Brighton line was in progress. He wrote in his diary 'the railway contractors would not buy my bricks unless they were compelled to do so, or let their works stand still'.

The bricks that were needed for tunnels, cuttings, viaducts, bridges, stations and other buildings were sourced from brickfields set up along the line, there was one, for example, at Balcombe.
Clay spoil extracted from tunnel and other excavations was used in brick manufacture. Then the clay returned to the tunnel in the form of the brick tunnel lining.
Molly Beswick whose excellent work 'Brickmaking in Sussex, a History and Gazeteer' is the definitive work on Sussex brickmaking believes there is a possibility that brickyards in Burgess Hill supplied some of the bricks for the section of the line from Cuckfield southwards.
Brick firing - kiln or clamp
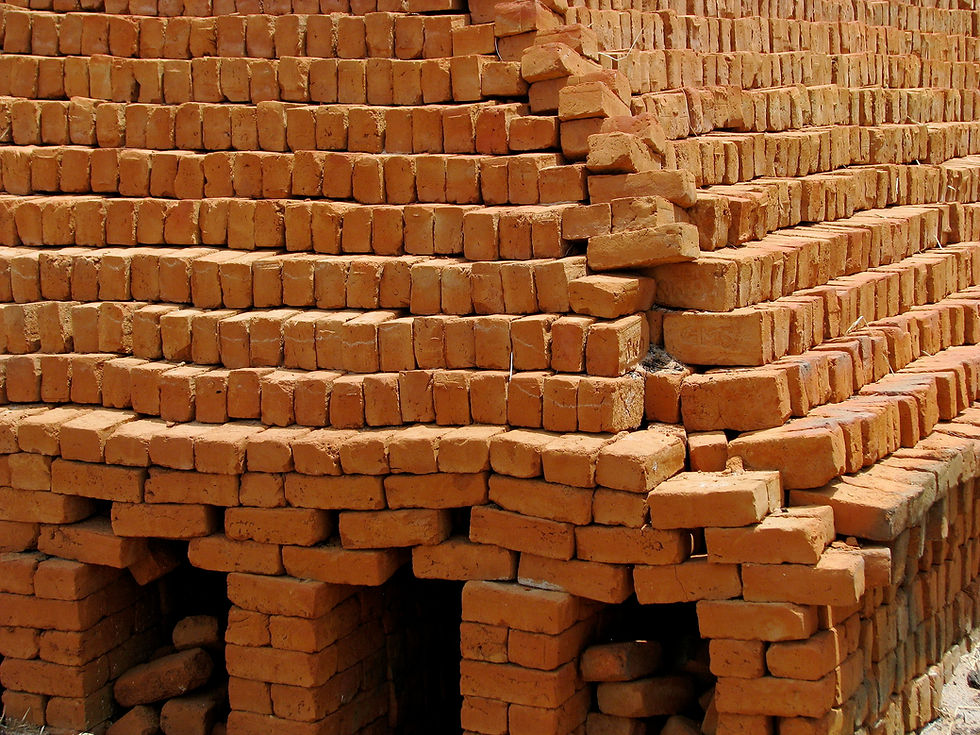
Most of the brick firing will have been done using brick clamps. A clamp is a temporary construction of unfired bricks which is usually dismantled after each firing. Clamps had level floors of burnt brick. Channels were made in the floor and filled with coke or other fuel. Clamps typically contain 30,000 - 150,000 bricks and take 2 to 3 weeks to complete the firing process.

Slow-burning in a brick clamp produces tough and strong bricks. It is a very cheap method of firing and a skilled workforce is necessary. Six to eight men during a summer season could produce a million bricks - sufficient to build 30 houses.
The bricks vary in colour depending on the heat they experience in the clamp and the type of fuel used. Colours can vary considerably with shades of red, with black and blue being present too. When bricks were sold on, they would be sorted and sold at different prices, depending on their quality and appearance.

Bricks with character
Today architects like to use hand made clamp-fired bricks as they add character and charm to a building. But the former are more expensive. Today's mass produced tunnel kiln bricks tend to be uniform in appearance and quality.
You may be interested to know that the Chailey brickworks, now owned by Ibstock Brick, is the oldest brickworks in the UK having been operational for 300 years. Today it is still selling clamp fired bricks.
More established early brickyards - and some established brickfields in Sussex would have used simple updraught or beehive kilns, while others moved on to downdraught more advanced and productive Hoffmann kilns.
As mass production took over, motor transport made it possible to move larger quantities of bricks more cheaply. Builders dropped brick production in favour of relying on experienced brick manufacturers to deliver more reliable and consistant products to their sites.
The following video from HG Matthews, Bellingdon, Chesham, is 11 min long. It has a slow start but has an interesting and productive conclusion. You may prefer to start 7mins from the start.
The Cuckfield Brickfields
Beswick’s book lists nine brickyards in the immediate Cuckfield area mostly to the north. The map here shows the spread of locations, but the 'kiln' icons show areas much larger than the fields themselves.
The 'TQ' grid references of the brickfields can be pinpointed using: https://gridreferencefinder.com

A. Brickyard NE of Handcross
Grid Ref : TQ 266 301
Date : Bricks were advertised for sale at Bigse's kiln in 1794. The yard was listed on the tithe award of 1843 but closed by 1874 when only Brickyard Wood remained
Operator : Joseph Biggs & Co. were the tenants in 1843
Refs: TDE 91; OS 6in 14 (1874); SWA, 18
Aug 1794.
B. Brickfield on the south bank of the river Ouse
½ mile north of Bigges Farm
Grid Ref : TQ 291 279
Date : Brickfield was listed on the tithe award of 1843: a possible alternative site for Bigse's kiln (cf site 1)
Ref: TDE 91.
C. Brickfield on Tys Farm east of Staplefield
Grid Ref : TQ286 280
Date : Listed as Brick Field in 1843
Ref : TDE 91.
D. Brickfield on Pains Place Farm SE of Ansty
Grid Ref : TQ 299 215
Date: Listed as Brick Field in 1843
Ref : TDE 91.
E. Brick kiln SE of Hatchgate Farm east of Cuckfield village
Grid Ref: TQ 315 246
Date: Listed as Brick Kiln Pit in 1843
Ref: TDE 91.
F. Brickyard on the east side of Ardingly Road
Grid Ref : TQ308 254
Date: Marked on maps of 1843 and 1874; called Longacre Brickyard in 1882 and closed shortly after this
Operator : Joseph Jeffery from at least 1843 to 1859 and Joseph Bacon Jeffery from 1862 to 1882
Refs : TDE 91; OS 6in 26 (1874); Kelly (1845, 1859-78); SWA, 28 Feb 1882.
G. Brickfield on the west edge of Gores Wood north of Cuckfield Hospital
Grid Ref : TQ 309 259
Date : Marked only on the map of 1874
Ref : OS 6in 26 (1874).
H. Brickfield on the east side of London Road
Grid Ref : TQ 307 253
Date : Marked only on the map of 1874
Operator : Possibly Stephen Knight, a builder and contractor at Whiteman’s Green, who advertised as a brickmaker in 1895
Refs : OS 6in 26 (1874); Kelly (1895).
I. Brickfield at Broadstreet west of the former gasworks
Grid Ref : TQ311 249
Date : 1882 - c1904
Operator : John Norris advertised in 1882 then by E. Norris & Sons in 1887 and Edward Norris in 1903
Product : Clamp bricks
Refs : OS 6in SW (1899); Kelly (1882-1903).
There are just as many brickfields in the Haywards Heath area.
Sources
'Brickmaking in Sussex, a History and Gazeteer', by Molly Beswick, Middleton Press 1993 . Illustration of Clamp also from this source.
Molly Beswick also wrote the history for Ibstock's Chailey website:
300 years of brickmaking: the Chailey kiln by Benedikte Ranum https://esibuilding.wordpress.com/2012/02/17/300-years-of-brick-making-the-chailey-kiln/
Brick clamp in rural India by McKay Savage from London. Wikimedia public domain image.
The bricks would be placed in the 'clamp', or kiln, for firing at Bottesford. From the excellent local history site: https://www.bottesfordhistory.org.uk/content/catalogue_item/bottesford-local-history-archive/photographs-of-bottesford-brickworks-during-the-edwardian-period
Building a clamp at Burnt House Lane, Shide, Isle of Wight https://www.iwhistory.org.uk/brickmaking
Video: Building a wood fired clamp https://youtu.be/s9W_ugPXqKk
How to deal with polluting clamp-type kilns Shanti Sustainable Energy Foundation https://issuu.com/ssefcommunications/docs/unclamping-india/s/10810741
The secret history of London brick https://londonist.com/2013/11/the-secret-history-of-the-london-brick
If you want to learn more about brickmaking why not visit the award-winning Brickworks Museum at Bursledon near Southampton. It is believed to be the UK's sole surviving Victorian steam-driven brickworks. Lots of activities for kids and there are steam days too.
Contributed by Malcolm Davison.
Commenti